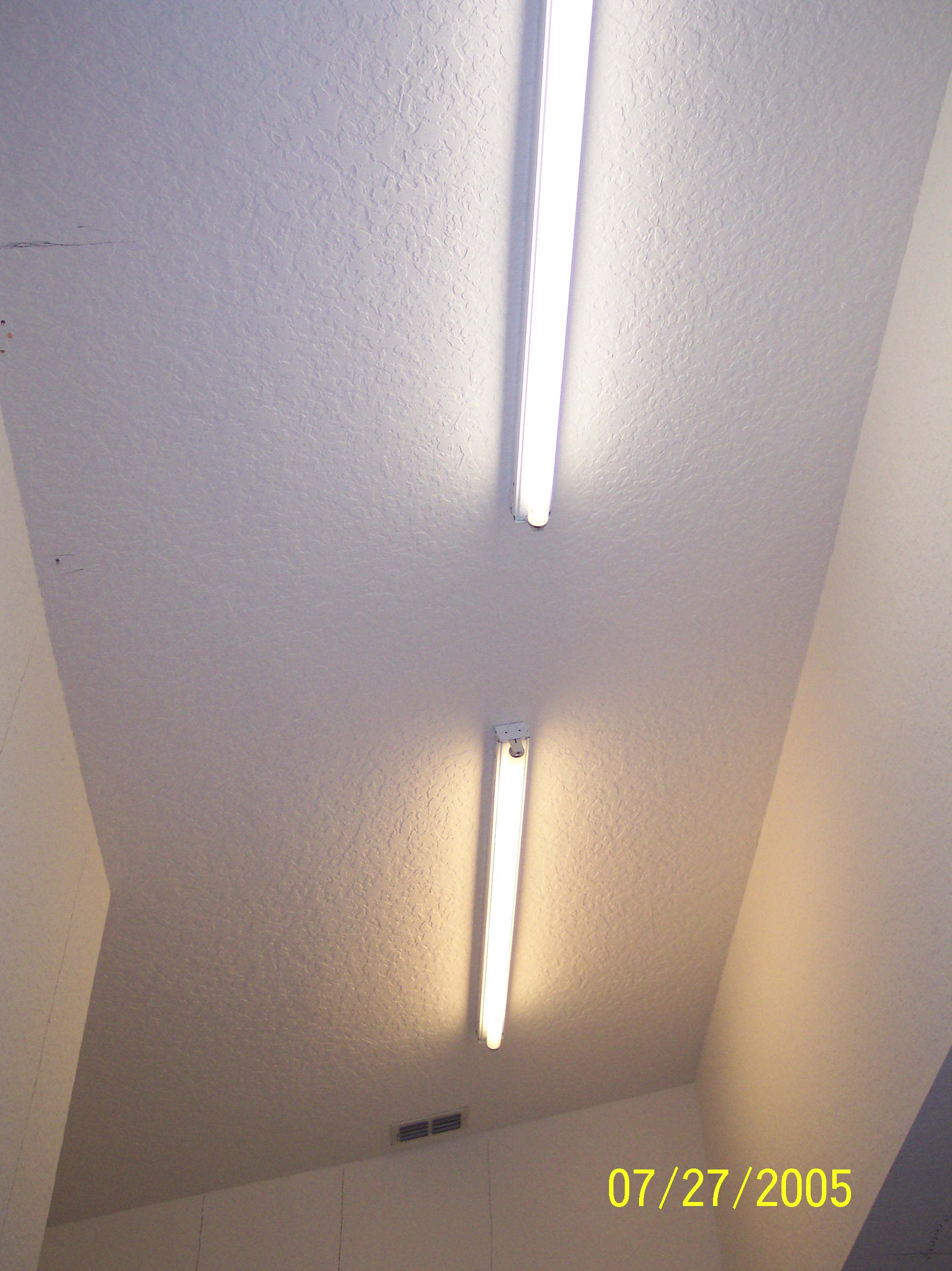
As you can see, we started with plain white walls and two unattractive 48"
fluorescent lights. The first thing we did was mark where all the
metal studs were located. Since there are no wood studs in the walls,
we weren't able to simply nail the cedar planks to the wall. Adhesive
was our best choice, but it could get quite expensive. So we got 1/4"
sheets of cheap plywood and covered the walls with it.
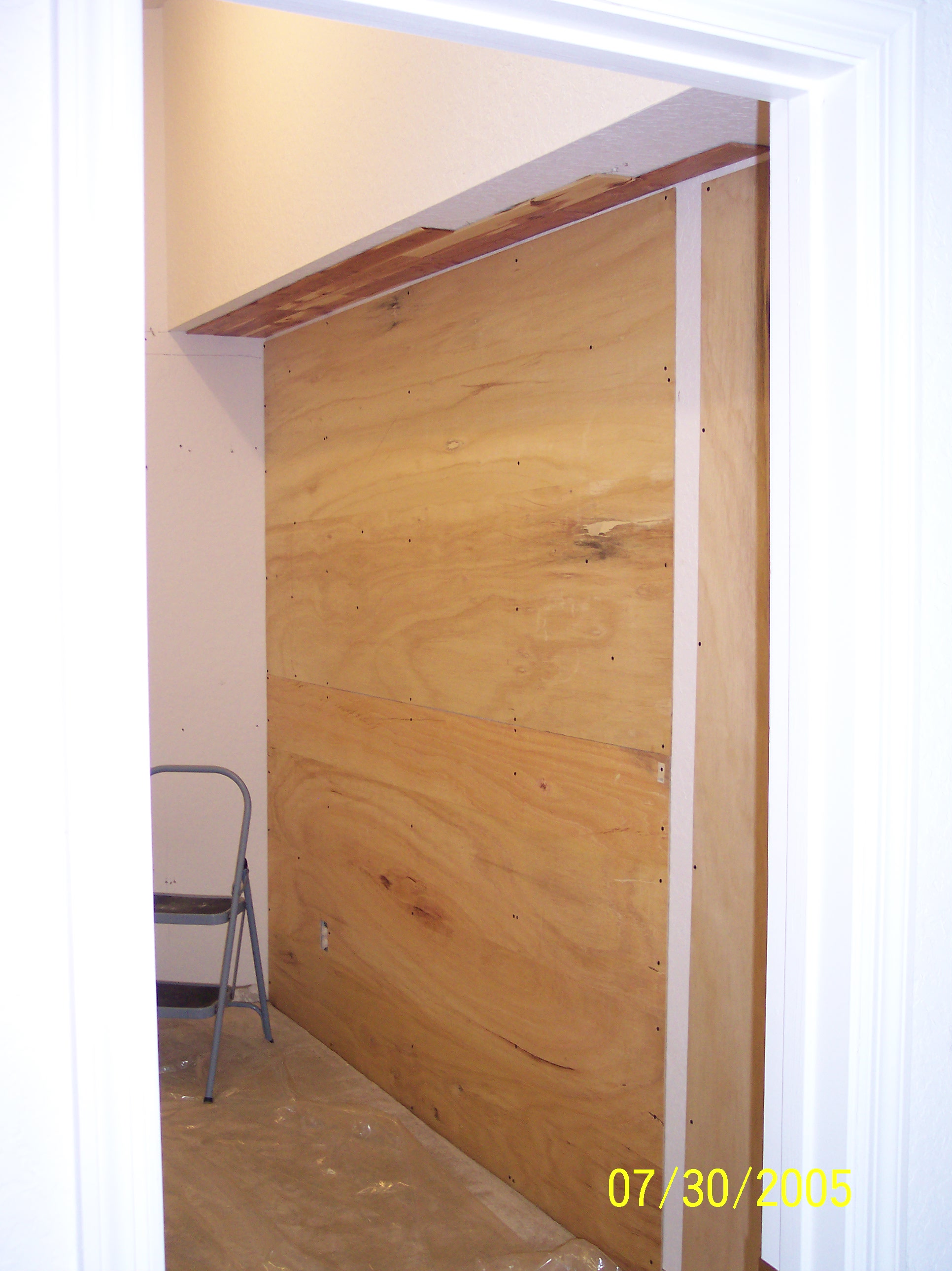
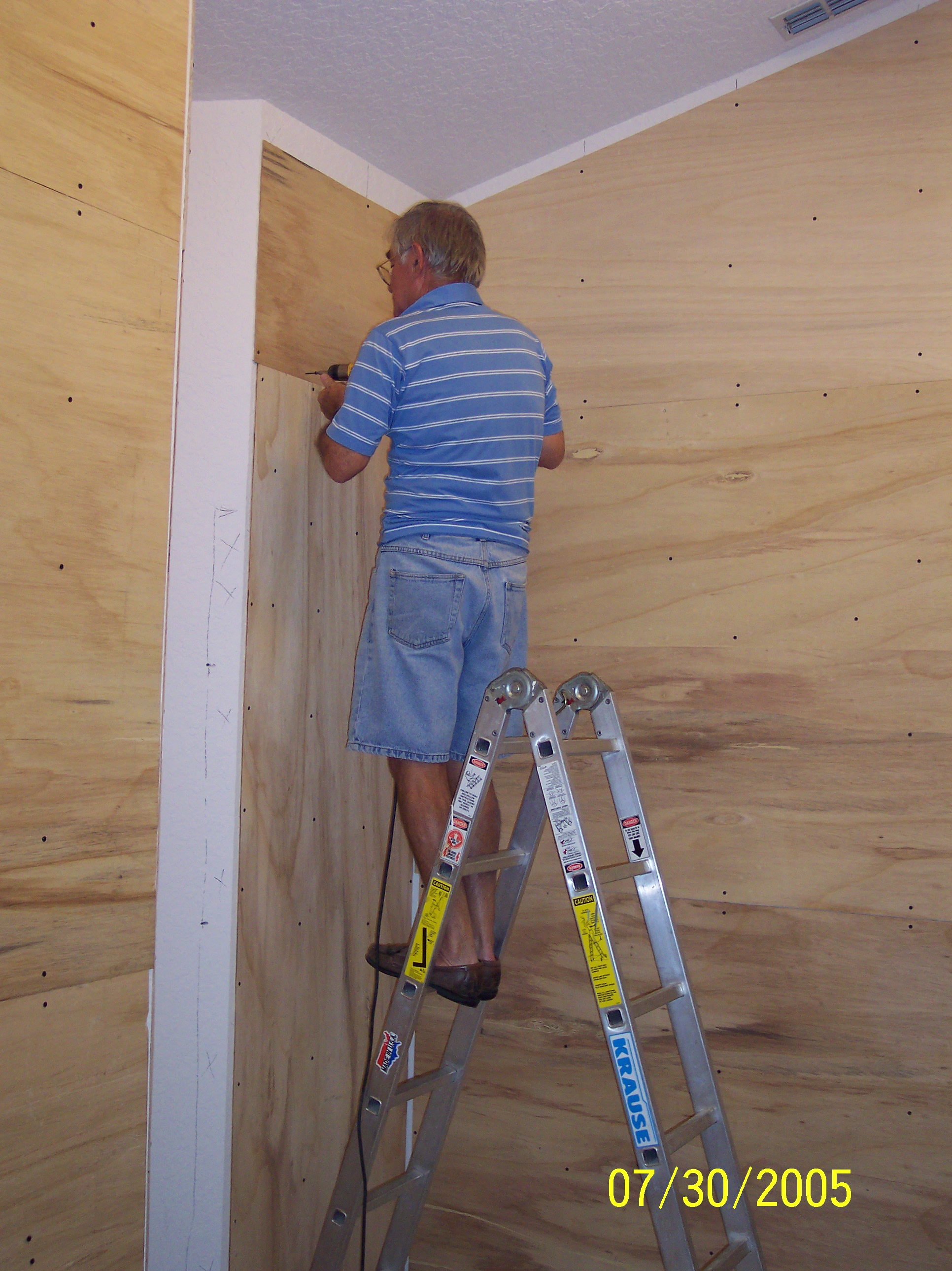
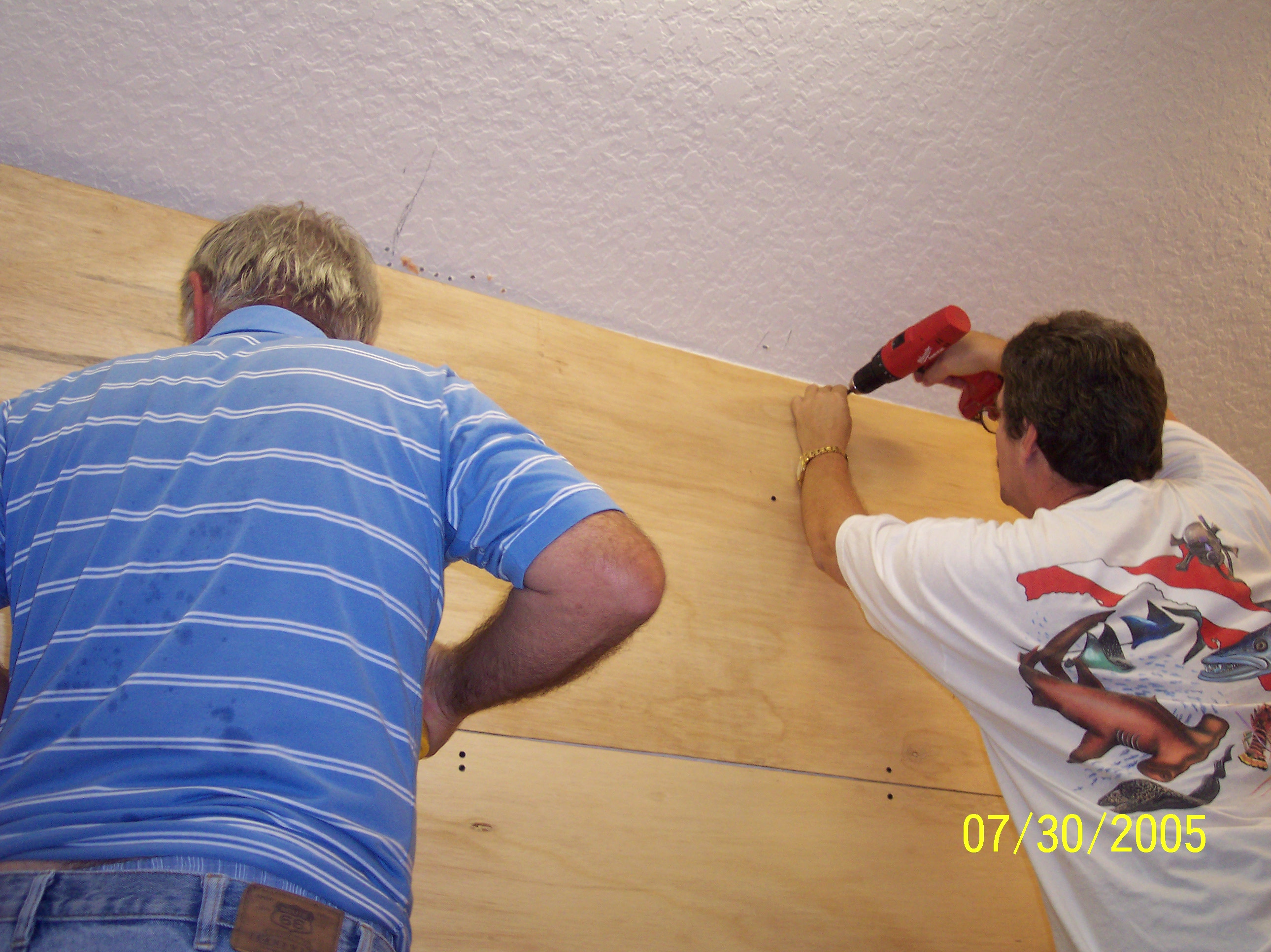

Michelle's dad, Bill, came over on the weekend to help, and boy are we glad
he did...this is really a two-man job, and with his help we knocked out in
two days what would have taken me two weeks to do by myself! The
panels were attached with construction adhesive and screws. No way
will these walls ever come down!
It was hard
work too! Measure, cut, fit, recut...and everytime a new cut had to be
made, it meant another trip out to the garage!
Harley
was so worn out he collapsed by the sliding glass doors!

We started attaching the cedar above the bumpout. Now that we had
something to nail to, we didn't have to use the adhesive so much, and things
began to move a little faster.
It was still hard work...at this point, everything was done from a
ladder...measure, mark, trot out to the garage to cut, bring it back to fit,
then glue and nail..move on to the next one. All the while trying to
maintain a random pattern to minimize the joints lining up. A major
problem was the fact that the cedar had warps and bends...a lot of it wasn't
straight, so we spent a great deal of time prying the tongues and grooves
together so they would mate.
The following show how the job took shape.
We did the walls first, but not quite up to the ceiling, then did the
ceiling last.
The picture below shows the angles of one wall in our closet that required
miter cuts on one edge to ensure a clean look. This was very
time-consuming, and took me the better part of two days to complete.

When I reached the lights, it became time to remove the fluorescents, and
install the track and pendants.
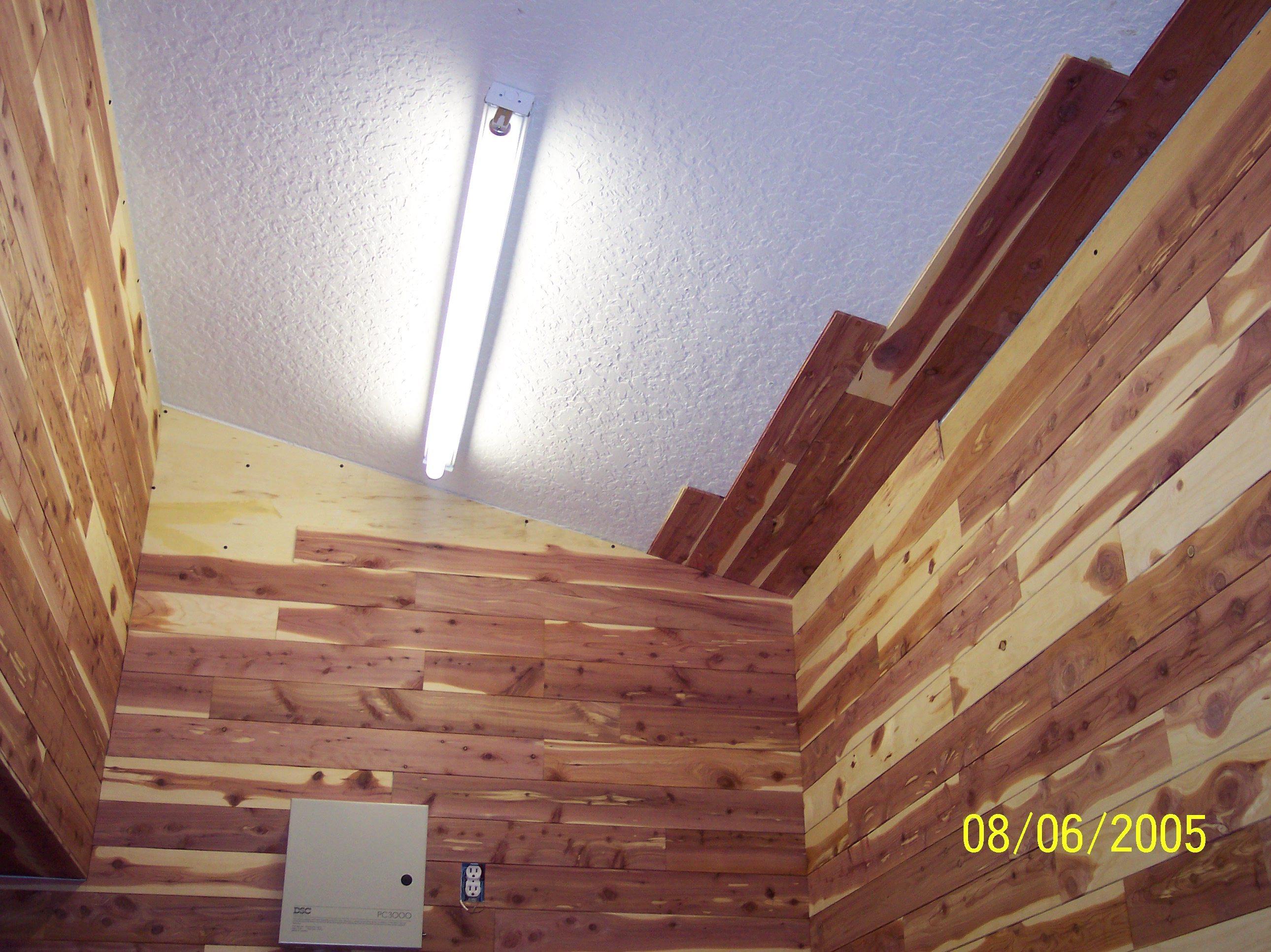
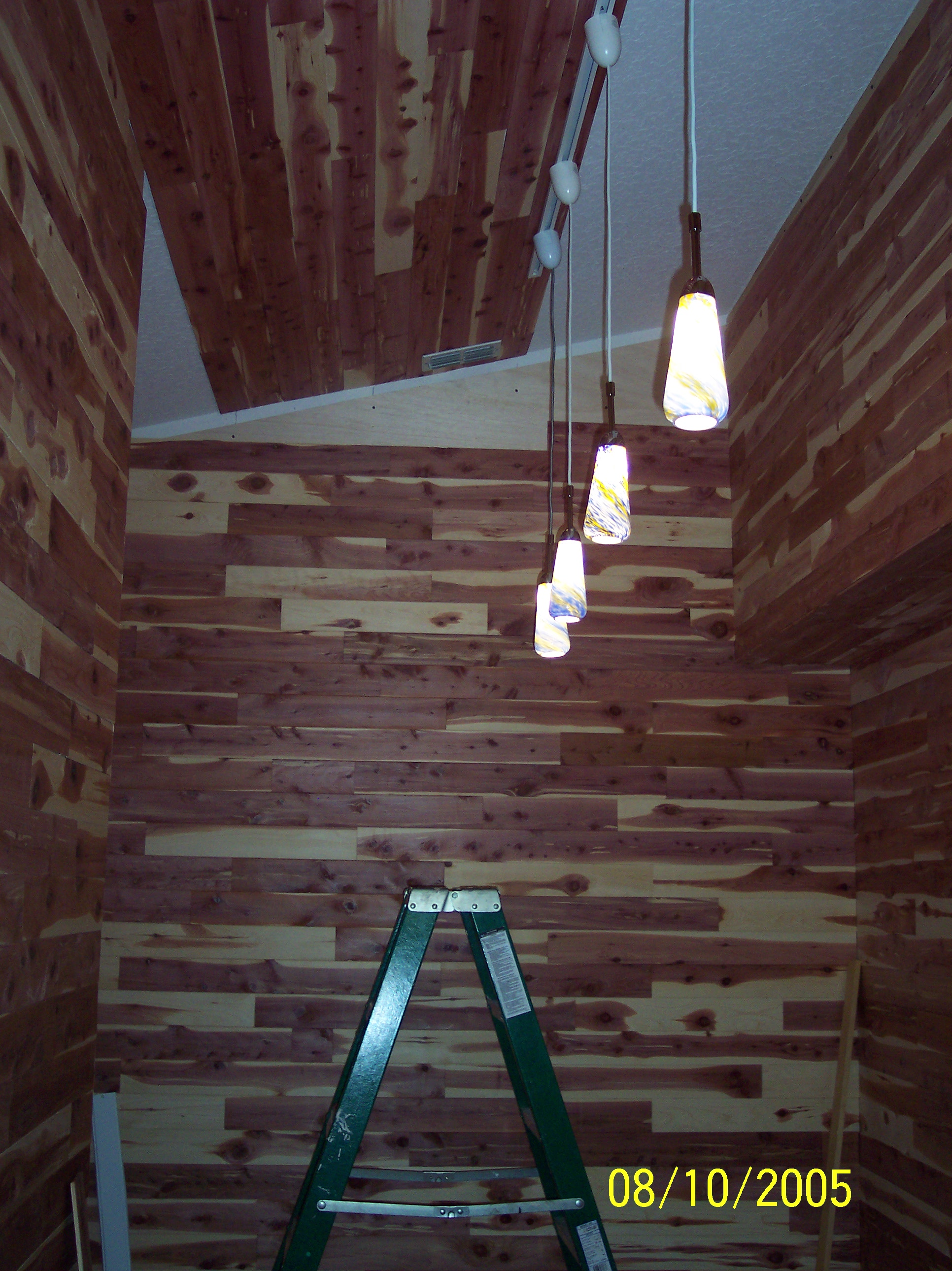
Starting on the ceiling, and as you can see, it's vaulted! Starting at
one edge and working across. The new pendant lights don't put out as
much light as the fluorescents, but heck, it's a closet! How much
light do you really need?
The last thing I did was replace the standard
light switch with a motion detector switch that turns the lights on whenever
you enter the closet, and turns them off shortly after you leave. It's
a great toy!
And finally, about three weeks after starting the
job, I finally placed the final piece in place. The last pictures here
show the results. It smells great too, by the way.
